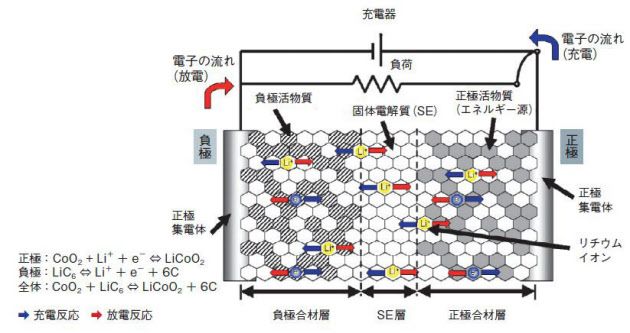
充放電時の電子の流れ。中央の固体電解質を介してリチウムイオンが負極と正極を往復する。既存のリチウムイオン2次電池の電解質は液体であり、これが低温や高温での動作を妨げている。全固体リチウム電池の固体電解質は、両極を電気的に分離するセパレーターの役割も担う(図:日立造船)
2018.07.25 朝日新聞 記事
↓
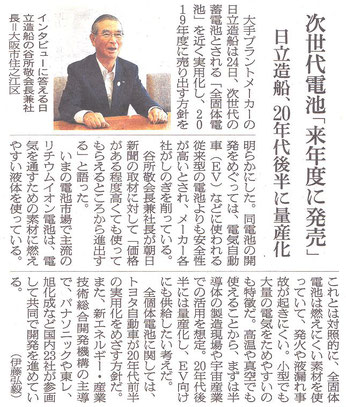
日立造船は、“ポストリチウム(Li)イオン2次電池”の有力候補である全固体電池を低コストに製造する技術を開発、開発品を公開した。
電気自動車・ハイブリッド車(HV)、家庭・企業・公共施設でのピークシフトやバックアップ用途(定置向け)、太陽光発電システムをはじめとする再生可能エネルギー発電所の出力安定用途などで、2020年以降、既存のリチウムイオン電池などを置き換えていく狙いである。
全固体電池は、既存のリチウムイオン電池では液体の電解質を固体にして、正極と負極を含めた部材をすべて固体で構成する。液漏れの恐れがない上、一般に電解質が難燃性のため燃えにくく、安全性が高い。電解質は、マイナス40℃といった低温でも凍結せず、100℃でもガスにならないため、幅広い温度環境で温度調整装置を使わずに利用できる。
また充放電時のイオンの移動が限られ、電極や電解質の劣化が抑えられる特徴もあるため、長寿命化しやすい。液体を使わないため、1つのパッケージ内で積層でき、高電圧化、大容量化しやすいといった長所もある。 現在、旭化成、日立製作所、出光興産、村田製作所、ソニー、太陽誘電、トヨタ自動車など多数の企業が開発にしのぎを削っている。
日立造船が開発した電池は、硫化物系の無機材料を電解質に使う点では、トヨタ自動車などの電池と変わらない。
特徴は製造手法にある。粉体の成型などに強みのあるグループ会社の技術を生かして、簡素に製造できるようにした。
「バルク型」と呼ばれる大容量の全固体電池では、電極と電解質を溶液にしてから塗布して乾燥する工程を繰り返していた。
材料に高圧をかけて電解質を両電極で密着させる必要もあった。日立造船でも、従来は10t/cm2(トン/平方センチメートル)の圧力下で製造する必要があり、充放電させるには600kg/cm2の加圧が必要だった。同社は、電解質と電極を粉体の原料のまま成型する技術を確立した。
成型工程で、高圧をかける必要はないという。粉体同士の密着性を高める技術を持つためだ。機械的圧力をかけない大気圧下で充放電が可能という。それでも固体電解質を薄くして抵抗を低減できた。 製造工程を簡素にできる分、信頼性を維持しつつ、製造コストを抑えやすい。
同社は、コストと信頼性を競合品に対する強みとして、早期の実用化を目指す。
まずは様々な応用分野へ展開できるように、円盤状のペレット形、薄い直方体の積層形を開発した。
これらを基に、2018年に電池メーカー向けに製造し、2020~2023年における市場での導入を期待している。
[日経エレクトロニクス2016年4月号の記事を再構成]
■重くしない強度維持策が必要
もっとも、量産に移行するまでには課題もある。
1つは、既存の開発品では両電極を挟み込む頑丈な金属板が必要なことだ。
外部からの力で破損しないようにするためである。エネルギー密度として明らかにした200Wh/kgは、金属板を含まない値。
金属板を含めたエネルギー密度が、セル当たりの金属板の枚数次第では半分程度になってしまう開発品があるという。
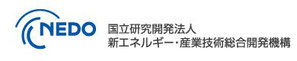
全固体リチウムイオン電池の研究開発プロジェクトの第2期が始動
NEDOは、世界各国でモビリティの電動化に向けた動きが活発化する中、高エネルギー密度化と安全性の両立が可能な蓄電池として注目されている全固体リチウムイオン電池を早期実用化するための研究開発プロジェクトの第2期をスタートさせました。
本プロジェクトでは、自動車・蓄電池・材料メーカー23社および大学・公的研究機関15法人が連携・協調し、全固体リチウムイオン電池のボトルネック課題を解決する要素技術を確立しつつ、プロトタイプセルを用いて新材料の特性や量産プロセス・EV搭載への適合性を評価する技術を開発します。また、日本主導による国際規格化を念頭に置いた安全性・耐久性の試験評価法を開発します。
さらに、研究開発と並行して、電動車両が大量普及する将来の社会システムのシナリオ・デザインを検討します。
【委託先】
技術研究組合リチウムイオン電池材料評価研究センター(LIBTEC)【代表機関】
(本事業に参画する組合員企業)(順不同)
トヨタ自動車(株)、日産自動車(株)、(株)本田技術研究所、パナソニック(株)、(株)GSユアサ、日立オートモティブシステムズ(株)、マクセル(株)、
(株)村田製作所、ヤマハ発動機(株)、旭化成(株)、JSR(株)、住友金属鉱山(株)、大日本印刷(株)、凸版印刷(株)、東レ(株)、(株)日本触媒、
富士フイルム(株)、三井化学(株)、三菱ケミカル(株)、(株)クラレ、日産化学工業(株)、出光興産(株)、三井金属鉱業(株)の23社
(国研)産業技術総合研究所、(国研)物質・材料研究機構、(国研)理化学研究所、
(地独)大阪産業技術研究所、九州大学、京都大学、群馬大学、東京工業大学、豊橋技術科学大学、名古屋大学、兵庫教育大学、北海道大学、
大阪府立大学、甲南学園、(一財)日本自動車研究所
※ メール・BLOG の転送厳禁です!! よろしくお願いします。
コメントをお書きください