接着の「見える化」
*狙うは革新的な軽量化、接着の「見える化」が設計を大きく変える
東京工業大学科学技術創成研究院教授の佐藤千明氏に聞く
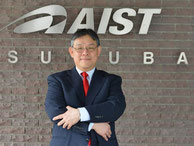
世界で「接合革命」が起きている。軽量化や材料の多様化により、これまでの溶接から接着剤への置き換えや併用が進んでいるのだ。接着技術で日本は世界をリードする。中でも、著しい研究成果を出しているのが、接着の「見える化」だ。
接着の見える化とは何か。
産業技術総合研究所(産総研)接着・界面現象研究ラボ研究ラボ長であり、東京工業大学科学技術創成研究院教授の佐藤千明氏に聞いた。
— 「見える化」レベルの向上で接着のメカニズムが解明されていると聞きます。接着剤に対するユーザーの信頼性や納得度が高まりそうです。
佐藤氏:その通りです。既に、金属と接着剤の界面については理解が深まりました。
今後はさらに、樹脂と接着剤の界面や樹脂同士の界面に関する接着のメカニズムが明らかになると思います。
すると、もっと大きな波及効果があることでしょう。軽量化の流れで、金属から樹脂への置き換えがどんどん進んでいっているからです。
実は、樹脂と接着剤の界面や樹脂同士の界面で起こっている現象をまだ誰も見たことがありません。
従って、より強固な接合を得たいなど、接着剤や周辺技術に技術的な改良を加えたい場合、現在は完全に勘と経験で、すなわち「こうなるだろう」という推定で技術開発を行っています。
しかし、最近は埋もれた界面の観察技術が登場したことにより、例えば界面で化学反応が起きているとか、分子間力でくっついているとかいったことが分かるようになりました。これは将来の接着剤の進化に非常に有効ですし、接着剤に限らず、樹脂同士の界面はいろいろな製品にあるので、その部分の接合強度や耐久性の改良などに大きく貢献すると思います。
— 樹脂と接着剤、また樹脂同士の接着のメカニズムはまだ解明されていないということですか。
佐藤氏:昔からいろんな説がありました。化学反応説や分子間力説、相互に樹脂が溶けて絡み合っているといった説などです。大体、樹脂の場合はこの3つが有力視されてきました。
これらの1つひとつは確からしいのですが、特定のケースの場合にどれが支配的かは意外に分かっていないのです。
これが明らかになれば、設計者などのユーザーは自信を持って接着剤を使うことができますし、接着剤や材料メーカーはより良いものを作ることが可能になります。
経験則から科学に立脚した接合面の評価へ
— 自動車や航空機などのユーザーの中には、接着剤がくっつき続けるかどうかに関して不安を感じる人がいます。 この不安を、界面の測定技術の進化が解消してくれるということですか。
佐藤氏:今後、そうなっていくでしょう。
例えば、最も厳しい条件が接着剤に求められる航空機分野では、既に米ボーイング(The Boeing Company)などが接着剤を使うか否かを判断する際に、接着剤とターゲット材料(接着させる材料)との間で共有結合が生じていることを非常に重視しています。
共有結合は、他の環境因子(例えば、水分の浸入)よりも結合エネルギーが大きいことが化学的に明らかだからです。
技術的な裏付けがとれれば、航空機メーカーも安心して接着剤を使えるというわけです。
一方、水素結合か分子間力の場合は、例えば水分が入ったときに、エネルギーの大きさが同じ程度だったり、親和力が似ていたりする場合は、水分で劣化するケースが考えられます。
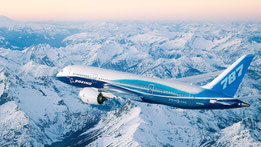
界面の接着メカニズムが明らかになり、しかも強固な接合力が作用していることがエビデンス(科学的な証拠)ベースで解明できれば、くっつき続ける環境劣化の要因が小さいものでも突き止めることができる。
すると、より信頼性が高く、安心して使える接合面を得られることにつながるのです。こうした界面での共有結合や化学反応などと湿熱耐久性などとの相関は、今まさにいろんな人が研究しているところです。
確実に言えるのは、今後は経験則ではなく、エビデンスベースで科学に立脚した接合面の評価が主流になっていくということです。今はその途上にあると言えます。
実はわが国でも、接着の見える化に関しては国家プロジェクトが動いており、新エネルギー・産業技術総合開発機構(NEDO)の支援の下、新構造材料技術研究組合(ISMA)にて、革新的新構造材料等の研究開発が実施されており、この中で構造材料用接着剤の開発が始まっていますし、同時に接着の基本メカニズムを同定する手法に関する各種の取り組みが実施されています.もう数年もすれば、界面の分析は当たり前の手法になり、そこから得られたいろいろな知見から接合強度を判断できるようになるでしょう。
*日本発、接着の「見える化」 設計革新を起こす5つの技術
— 界面の状況が見えるようになり、接着剤のメカニズムがよく分かるようになった。従って、今後はより使いやすい接着剤が出てくる可能性がある。 ISO(International Organization for Standardization;国際標準化機構)化の動きも出てきた──。ここまでの話を振り返るとこうなります。 では、ユーザーが接着剤をうまく使いこなすために必要な課題は何でしょうか。
佐藤氏:2つあります。1つは、接着剤を使った接合部の設計に慣れてもらうことです。
というのも、接着剤の強度評価の規格は溶接や材料のそれとはかなり違っているからです。しかも、まだ十分に完成された世界ではありません。接合部の強度設計に関して、より正確な設計法を確立する必要があるため、まだまだいろいろな規格を作っている段階です。
加えて、接合部の耐久性の保証法を確立する必要があります。ここがまだ完成したとは言い難く、発展途上というところです。その理由は、我々は「実験力学」と呼んでいるのですが、実験的に強度のパラメーターを求めるのは接着の場合、とても難しい。そもそも計測しにくいターゲットなのです。
例えば、接着の界面の強度を調べるときには破壊エネルギーというパラメーターを調べなければならず、これを求める規格にはDCB(Doble Cantilever Beam;双片持ちはり)試験片を使います。2枚の板を貼り合わせて離していく試験片です。測定時に加わった力と亀裂(クラック)を同時に計測しなければなりません。
ところが、このクラックの先端が見えにくくて世界中の技術者が困っており、世界で同じ実験をしているのに結果が違っているのです。こうしたところには最新技術を導入し、正確に測れる技術を研究しなければなりません。
幸い、産業総合研究所には「応力発光材料」という特殊な材料を開発したグループがあり、対象に塗るだけで応力集中点やクラックの先端が光って目で見える新しい技術を開発しました。この研究はNEDO(新エネルギー・産業技術総合開発機構)のプロジェクトでも引き続き改良を行っており、これを使えば、世界中で誰が行っても同じような結果が得られるようになります。
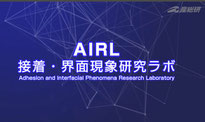
1. 力学的評価
2. 異種材料の接着メカニズムの解明
・和周波分光
・ラマンイメージング
3. 電子顕微鏡による接着界面の解析
4. 接着剤機能における化学的組成や化学反応に基づく考察
5. パルスレーザー走査法による接着接合部の超音波検査
6. レーザー誘起ブレークダウン分光による表面検査
7. 応力発光技術—ひずみ分布の可視化が開く検査・設計・予測の革新
8. 接着検証のシミュレーション
— 技術が進化しているので、ユーザーは接合部に慣れろということでしょうか。
佐藤氏:試験規格自体は研究者がきちんと確立することが求められます。
応力発光材料のような最新技術を使って研究結果をきちんと規格化し、ユーザーにはそうした規格に慣れてもらって、実験で出てきたパラメーターを勉強してもらわなければなりません。しかし残念ながら、現時点では規格も不十分だし、使い方を教えてくれる人がいないという問題があります。
ただ、日本接着学会などが接着の接合部に関する設計法の講習会やセミナーなどを積極的に開催しているので、そうしたものを利用するとよいでしょう。
また、将来的には接合部の設計に関してきちんとしたフレームワークを確立しようと我々は計画しています。
ISOの資格などを取得した人はしかるべき能力があると認定できる。従って、そうした資格を目指してもらうことなどを通じて、フレームワークを作っていきたいと考えています。
出典:日経 xTECHから一部抜粋

見える化は簡単なのかもしれないけれど……
IoT(モノのインターネット)のビジネス活用で、最初のステップと言われる「見える化」。
よく、「見える化」は簡単だけど、見える化した後、見える化した次をどうしたらよいか分からないということを耳にします。
過去、数年にわたり、工場の見える化を進めてきて、一定の成果を挙げているにもかかわらず、「まだまだ見える化が足りない」・・・具体的には、「人の見える化」がテーマで、現在、営業部門などでの“人の暗黙知”を“形式知”へと見える化するための取り組みを進めていると、ある大手企業の経営トップは言います。
「見える化しても、その次の活動に困っているという話もよく聞きますが?」と問うと、
「見えないことには、次の手が打てない。見えさえすれば、問題に対して対処、適応ができる」と事も無げに返されました。よくよく考えると、当たり前の話です。
見える化とは、課題を抽出、見える化することで、課題さえ見えれば、その対応策もおのずと見えてくるはずです。見える化しても打つ手に困るようであれば、見える化自体がうまくいっていないということなのでしょう。または、見える化に対して課題の抽出ではなく、課題解決策が出てくるものだと過剰な期待を寄せてしまっているということかもしれません。
※ メール・BLOG の転送厳禁です!! よろしくお願いします。
コメントをお書きください