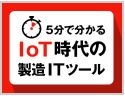
インダストリー4.0、インダストリアルIoT(モノのインターネット)の時代を迎え、製造業のためのITツールもその役割を変えつつあります。
IoT時代のCAD
機械系の製造業と建築・土木業界では長らく、部品や製品の設計のために、紙の図面が用いられてきました。その後、コンピュータの機能を利用し、グラフィックス画面に2次元で直線や円弧を作図できるようになったため、2次元のコンピュータ製図機能が誕生し、このときにCAD(Computer Aided Design:コンピュータ支援設計)という言葉も生まれました。CADによってデータ化されたことで、類似派生図面や正確な寸法記入、プロッターによる正確な描画が可能となりました。現在においても2次元CAD(2D CAD)は機械図面、建築図面などの作成に広く用いられています。
その後、部品の切削加工、また3次元構造解析などの理由から、2次元ではなく3次元で部品や製品を表現するニーズが高まりました。2D CADが線画であったのに対して、3次元の物体を正しく表現するためには、頂点、稜線、面(平面および曲面)、物体内部(どちら側にモノがつまっているか)などより多くの情報を表現しなければなりません。また、部品によっては非常に複雑な形状となりますが、コンピュータ技術の進化により、複雑な情報処理が可能となりました。
また、3次元モデルの定義のため、3次元モデル同士の和/差/積をとるブーリアン演算、主要部から詳細部への定義順番を履歴として保存し、主要寸法を修正可能で、必要があれば履歴をさかのぼって形状を変更できるパラメトリック・フィーチャーベースモデリングなどの技術が開発されました。 また、複数部品から成る製品のため、各部品の配置情報を保持し、かつ階層構造で製品全体を定義できるアセンブリという概念が導入され、大規模な製品全体を3次元CAD(3D CAD)で表現できるようになりました。 これらの技術により、部品の3次元モデルデータを基に加工パスを算出する3D CAD/CAMシステムが誕生しました。
また、3次元モデルは構造解析にも活用されるようになりました。
この他、3次元モデルデータは、樹脂や鋳造で成形される場合の金型設計にも用いられています。また、製品の複雑化、多部品化に伴い、部品同士がぶつからないか、適切な距離をとっているかという干渉チェック/クリアランスチェックにも3次元の部品形状が利用されています。
最近では、2次元図面で定義していた公差情報を3次元モデルに直接適用し、組み付け公差の解析や、製造された製品モデルの検査に利用するようなケースもあり、 3次元モデルは設計開発/製造における非常に多種多様なプロセスで活用されています。
これからのCAD
物理実体を表現してそれを活用する領域は既にほぼカバーされた感があるCADですが、デジタル化や自動運転、IoTがトレンドとなる時代の中で、CADも今までと異なる役割を担うようになっています。
3D CADは従来機械設計の領域でしたが、これからの時代は複合領域の設計や生産側にも活躍の幅が広がり、IoT時代のモノづくりにも貢献していくことになると考えられます。
IoT時代のCAE
CAEの根本となる理論や手法は多々ありますが、適用範囲が広い強度/応力解析の分野では、連続体である弾性体(応力とひずみが比例する前提)を対象とした材料力学が基盤となります。 任意の3次元形状に対しての理論式というものは存在しないため、そのような問題には離散化等数値解析的な手法を取る必要があります。1940年代にリヒャルト・クーラント(Richard Courant)が提唱した、連続体を三角形に分割する手法が、今日もCAEで用いられる手法の原点となっています。1960年にレイ・ウィリアム・クラフ(Ray William Clough)は「有限要素(Finite Element)」という用語を定義し、1960年初頭から有限要素法(FEM:Finite Element Method)を取り入れた商業CAEソフトウェアが販売されるようになりました。中でも有名なものがMacNeal-Schwendler Corporation(MSC)が開発した汎用FEAコードで、これが後の「MSC/Nastran」となりました。
1990年代後半以降、エンジニアリングワークステーションからPCへのダウンサイジング、またハードウェア自身の高性能化、並列化によって、非線形など高度な解析も、専用ハードではないより一般的な環境で実現できるようになってきています。
1970年代以降、部品/製品形状を定義するソフトウェア(CAD)が発達し、CAEの元となる3Dモデルの作成/調整が容易になってきました。また近年ではCAEソフトウェア自体の使い勝手の向上やCAD/CAE統合環境の開発により、設計者が設計段階で「設計者CAE」も盛んになっています。
これからのCAE
昨今、自動車業界では、自動運転を含むADAS(先進運転支援システム)の研究が盛んです。自動運転を実現するためには、膨大なデータの蓄積を必要としますが、そこで有効になるのがコンピュータ内の仮想環境で仮想の試験車を走らせる走行シミュレーションです。
・・・ 構成要素のモデル化から自動車1台を1DシミュレーションによってCAEモデル化するケースを取り上げましたが、今後はモデルや挙動について、データの集積から機械学習やディープラーニング(深層学習)を活用して、シミュレーションモデルやシミュレーション自体を高度化することが考えられています。
ディープラーニングについては各所で取り上げられているのでここでは詳述しませんが、言語処理、画像認識の分野で徐々に実績を上げています。CAEの分野、特に熱流体や燃焼系など複雑な解析においては、初期条件と解析結果の優劣との因果関係を発見するのが困難で、CAEを用いても性能向上につなげることが難しかったのですが、ディープラーニングを利用することでより短期で、目標性能を実現することが期待されています。
製造業の最近のトレンドとして、IoTやビッグデータ、AIなどが取り沙汰されています。そんな中でも、実は比較的古典的な概念であるCAE/シミュレーションモデルの利活用は、今後ますます重要になってくると思われます。
IoT時代のデジタル製造
CADが「何を作るか」を定義(設計)するのに対し、デジタルマニュファクチュアリングは「どうやって作るか」を定義するためのツールです。しかし、CADのように比較的明確な概念と違い、デジタルマニュファクチュアリングにはさまざまな側面があります。それに従ってITツールもいろいろありますが、既存のものは主に次のカテゴリーに分類できます。
- 部品あるいは金型の切削加工
- 組み立て(機械、あるいは人間による作業)、搬送工程
- 全体の工程/製造ライン
それぞれ項目において、設計(計画または定義)と検証の両方の側面があります。
製造工程のためのITツールとしては、生産のスケジューリングや製造実行システム(MES)などもありますが、それより上流、生産準備などと呼ばれる領域について述べます。
部品あるいは金型の切削加工ですが、これは航空機分野を端緒に、歴史的には最も早く開発された分野といえます。工作機械で素材を加工し、ほしい形状を得るためには、切削工具の移動(カッタパス)を工作機械に指示しなければなりません。
3D CADの進歩により、部品/金型の3D形状が定義されるようになり、それにつれて3Dデータを利用して工作機械の数値制御(Numeric Control)技術を活用するCAM(Computer Aided Manufacturing)ソリューションが進化し、加工プロセスの計画(Cutter Path Planning)/検証が自動化されました。
組み立て(Assembly)は、ある工程における組立順序、用いる機械(ロボット)の動作指示とシミュレーション、人間であれば作業工程の計画と検証を行います。
機械のシミュレーションであれば動作干渉、人間であればエルゴノミクスによる作業負荷が検証の対象になります。
加工も含めた組み立ての工程は、通常MBOM(Manufacturing BOM)またはBOP(Bill of Process)、日本語では工順/工程表として定義、管理されます。
多くの場合、これらは設計側で作られるEBOM(Engineering BOM)と構成が異なりますが、BOM同士の関係性を適切に定義することで、不具合課題の追跡、対策、また新製品の製品構成に対する生産側での対応を効率化できます。さらにはマスター工場でのマスター工程をグローバルの他生産拠点に展開する上でも、BOPの管理は有用となります。
これからのデジタルマニュファクチュアリング
1.バーチャルコミッショニング
生産システムにおいて、機械はPLC(Programmable Logic Controller)などによって制御されています。プログラミングされたPLCからバーチャル(仮想的)な機械を動作させることにより、実際に近い形で検証を行うことが可能です。
バーチャル環境での検証がOKであれば、制御対象を現実世界の機械に切り替えれば正しく動作するはずです。この手法はバーチャルコミッショニングと呼ばれ、生産ライン立ち上げの短期化、高品質化に寄与します。PLCは現実のものが使われる場合、またはエミュレーション機能によりソフトウェア上で行う場合もあります。
2.VRによる生産計画
製品設計側での使い勝手や視野を検討するためのVR(仮想現実、バーチャルリアリティー)利用は広がっていますが、生産計画でも同様に、工場や機械を3Dモデル化し、ウォークスルーを視覚体験できる環境が実用化されています。これによりさらなる生産性向上を図り、また立ち上げ後の改修・調整工数を低減できます。
また、現況の工場建屋、設備を3Dモデル化するために、カメラによる3Dスキャン(点群)を用いることが可能です。スキャンされた点群とCADで定義された設備モデルを同一3D空間で併存、検討することも可能です。
3.人間と協業するロボット
従来、ロボットなどは、安全の観点から安全柵内に配置し人間と隔離されており、ロボットの動作中、人間は柵内立ち入り禁止となっていました。
しかし最近は、ロボット技術の向上と生産性の観点から、人間とロボットを同じ空間内で作業させるための取り組みが進んでいます。その場合、人間の動きと、ロボットのそれをシミュレーションし、安全性を確保する必要があります。人間とロボットの可動空間、またロボットの移動速度からリスク調査を行います。
4.クローズドループマニュファクチュアリング(製造)
センシングや無線ネットワーク技術、データアナリティクスを活用して、モノの生産現場や使われ方の情報を多岐にわたって収集し、洞察を得るアプローチがIoTとして脚光を浴びて久しいですが、真に重要なことは、そこで得られた知見を素早くかつ的確に上流にフィードバックすることになります。
そのためにはデジタルデータプロセスの流通のためのプラットフォームを上流から下流にわたって備え、機械やBOPのデジタルデータにフィードバックを反映させることが重要になります。これが今後のあるべきモノづくりの全体像です。
フィードバックは下流から上流に展開されるため、これをクローズドループマニュファクチュアリングと呼びます。デジタルマニュファクチュアリングは真ん中の箱(生産計画のデジタルツイン)を担います。
IoT時代のPLM
データとプロセスを管理するIT基盤となるPLM(Product Lifecycle Management:製品ライフサイクル管理)を取り上げます。製品ライフサイクルとは、個々の製品そのものの「企画→設計→生産→販売→メンテナンス→廃棄」に着目する場合と、商品/マーケットの「上市→市場拡大→成熟→衰退」に着目する場合とがあります。ここでのPLMソフトウェアあるいはPLMプラットフォームは主に前者を扱います。
製品ライフサイクルにおいて、図のように会社に収入あるいは支出(コスト)がもたらされます。
製品ライフサイクルにおける企業の利益最大化
PLMの概念の先駆けは、1950年代に米国国防総省によって開始された構成管理(Configuration Management)です。この構成管理は、システムのライフサイクルに適用され、システムのパフォーマンス、機能、及び物理的属性の可視性とコントロールを提供しました。また、提案された設計変更が、全体に与える悪影響を最小限に抑えるよう、体系的に検証することに役立ちました。1970年代には、構成管理に寄与する多くの標準が策定されました。それらは同時に製品品質、相互運用性にも着目していました。
より戦略的なアプローチとしてPLMが使用されたのは、1985年アメリカン・モーターズ・コーポレーション(American Motors Corporation、略称AMC)が初めてといわれています。当時AMCは、自社よりも企業規模が大きい競合と競争するために「ジープ・グランド・チェロキー」の生産プロセスを加速する方法を模索していました。
PLMを使用すると、全てのデザイン、図面、及び関連書類が、研究開発/設計/製造など関係する部門がアクセス可能な一元化されたデータベースに格納されます。これにより、設計上の課題がより迅速に解決され、またコストのかかる設計変更が削減されることが期待されました。1987年にクライスラー(Chrysler)がAMCを買収したとき、PLMを活用した開発が非常に効果的であったので、そのプロセスを維持することにしました。
基礎技術の観点では、リレーショナルデータベースの改良とクライアント/サーバ技術の進歩により、柔軟かつ拡張性の高いシステムが可能となり、グローバルなPLMシステムの基盤構築が可能となりました。
また、2000年代のWeb技術の進歩、2010年代のモバイル/クラウド/UXの発達により、PLMの複雑な情報がグラフィカルにより幅広い環境からアクセス可能となりました。
一方、ITツールという観点では、1980年代から現存するグローバルCADベンダーがPLMの開発に注力してきました。当初はCADデータを対象としたPDM(Product Data Management:製品データ管理)が製品化され、その後に製品のライフサイクルを業務プロセスの流れや変更管理など含め一元的に管理するPLMとして進化していきました。
このために、各ベンダーは2000年代から積極的に生産準備や解析ツールに強みを持つ他社との買収/統合を進め、PLMベンダーとしての地位を確立しました。
これからのPLMの方向性
産業IoT(モノのインターネット)やインダストリー4.0などの変革の概念、ビッグデータ解析や人工知能などの革新技術によって、PLMも大きく変わろうとしています。また、生産現場のネットワーク、通常環境の無線技術、クラウド環境の進歩により、製品を作る現場、あるいは製品が使われている現場からのデータ集積、知見は爆発的に増加しています。そこから、バリューチェーン上でより良い価値を創造するためには、製品ライフサイクルの各所において、現場からのフィードバックを基に、デジタルモデルに対して有効にシミュレーションが実行される必要があります。
つまり、フィードバックループが形成され着実に実行されることが重要です。
有効にシミュレーションされるためには、製品全体のシミュレーションが可能なモデルが必要となります。
また、新技術/コンセプトに基づく製品がどのくらい収益に貢献するか検討するためには、製品だけではなく生産設備/ラインのデジタルモデル化も重要です。
どの既存生産設備を利用すべきか、あるいは新設しなければならないのか、既存の設備を活用するとして、どの程度の時間とコストをかけて修正すれば量産化できるのか、素早く複数案を検討するためには生産設備/ラインのデジタル化が不可欠です。
生産現場は現場調整が多く、扱う設備の数が膨大となることもあり、最新の正しい生産デジタルモデルが定義されていることは少ないですが、最近の3Dスキャン技術の活用により生産設備/ライン全体のデジタル化も可能になっています。
それらのデジタルモデルは、工程、設備を含めた工場の構成ツリー(生産BOM)としてこれからのPLMの中核を担うと考えられています。
工場のデジタルモデル例 出典:シーメンス
IoT時代のMES
製造実行システム(MES:Manufacturing Execution System)について紹介していきます。 PLMは製品ライフサイクル全体をカバーするものですが、ではPLMとMESは何が違うのでしょうか。PLMは、「何を作るか」「どのような設備/工程で作るか」を司り、基幹業務システムであるERPが生産計画を行います。
しかし、実際に生産現場を動かすためには、製造設備や検査機器とシステム的にリンクし、作業実施を監視/管理する仕組みが必要となります。
一般的に製造業の管理層は以下の3層に分けられます。
なぜ「計画(管理)」と「実行(工場)」の2層ではなく3層になるかというと、工場の中にも、工場の管理者と、ショップフロア(作業現場)の実行責任者がおり、その2者の間で、同様に計画指示と実行報告がなされるためです。上の3層と、個々に対応するシステム名を併記すると下図のようになります。
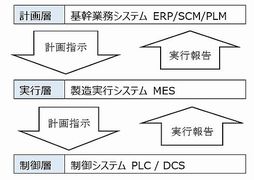
第2層に当たる工場管理者のためのツールがMESとなります。MESが担う具体的な役割は、一般的にMESA modelとして定義されています。
MESのコンセプトは20年以上前に提唱されたものですが、製造要件から高度な機械化が求められる石油/化学業界、半導体や液晶工場では浸透しました。ただし、一般的な製造業で見た場合、既存設備のインタフェースや工場ネットワークが課題となり、必ずしも浸透しているとはいえない状況です。
これからのMES
昨今のセンサー、ネットワーク環境の進歩により、設備インタフェースや工場ネットワークの課題が徐々に解決されています。つまり、工場内で移動する作業対象(ワーク:原材料や中間製品)の現況や、設備/作業者の稼働状況がリアルタイムで把握可能になり、MESを中核としたつながる工場の素地が整いつつあります。
・・・ IoT化で製造業におけるMESの役割や範囲は大きく拡大することが期待されます。
※ メール・BLOG の転送厳禁です!! よろしくお願いします。
コメントをお書きください