技能継承は「一回やれば終わり」じゃない
定着化に必要なデータ活用の仕組み
2024年06月27日更新
[池谷翼,MONOist]
国内製造業にとって喫緊の課題の1つが「技能継承」だ。これを支援するデジタルサービス、ツールも多く登場しているが、必要なのは長期的視点で技能継承の活動を続けられるか、という視点だ。デジタル技術を活用しつつ、技能継承を長期にわたるプロジェクトとして走らせる上で必要な取り組みを聞いた。
国内製造業にとって喫緊の課題の1つが「技能継承」。熟練者が定年退職などで企業を去ることで、現場で必要な技術やノウハウが若手技術者へと十分に継承されないリスクが高まっている。この中で、AI(人工知能)などデジタル技術を活用した技能継承支援サービスも登場している。現場で脈々と受け継がれてきた暗黙知を、映像解析や自然言語処理技術などを通じて可視化し、形式知化する。ロボットなど自動化機器導入による省人化も重要な一手だが、現実には人手で担う必要のある現場業務も多い。人から人への迅速な技能継承を実現する上では、こうしたサービス、ツールを活用していくことも大事だろう。
ただ気を付けたいのが、技能継承は一回施策を実施したら、一度ツールを導入したらそれで終わり、ではないということだ。
当然だが、人材を育てるには中長期の時間が必要になる。そのためには、技能継承のデジタル化だけでなく、プロセス自体をいかに組織に定着化させるか、という視点が必要ではないか。
デジタル技術を活用しつつ、技能継承を長期にわたるプロジェクトとして走らせる上で必要な取り組みとは何か。
製造業のスキルマネジメントツール「スキルノート」や、技能継承活動の立ち上げ支援サービスを展開するSkillnote 代表取締役の山川隆史氏と同社 社長室 マネジャーの高木孝介氏に話を聞いた。
「全てのスキルを伝えなければならない」という思い込み
MONOist 製造業の技能継承向けのデジタルサービス、ツールが多く登場しています。
高木孝介氏(以下、高木氏) さまざまなITベンダーが、暗黙知を形式知化するデジタルサービスを市場投入している。
AIがベテラン技術者の動きを観察して、若手の動作との差異を可視化するといったソリューションが、一部の先進的な企業で導入され、浸透し始めてきているようだ。
しかし、技能継承のプロセスを継続的にPDCAサイクルのもとで回すべきだ、といった視点を持つ製造業はさほど多くない。従来の「先輩から自然と学ぶ」という方法にしろ、浸透し始めたデジタルツールを活用するにしろ、今は良くても何十年かすれば同じ問題が起こる。
長期的な視点で、自分たちの継承の成果を定期的に評価し、取り組みにフィードバックする仕組みが大事だ。
ここでは技術や知見などを合わせて、スキルと表現したい。製造業でのスキル継承でよく誤解されるポイントが2つある。
1つは、技術が全て企業内にあるとは限らない点だ。外部企業に業務の一部を委託しているところもあり、モノづくり全てを内製化しているわけではない。
もう1つが、「ベテラン社員の全てのスキルを伝えなければならない」という思い込みだ。
本来は、どのスキルを次世代の社員に受け継ぐべきかを決定し、計画的に実行していかなければならない。
継承後には、継承のプロセスが効果的だったか、本当に継承の優先度が高い技能だったかを検証すべきだ。
計画と実績にギャップがあったなら、その知見をそれ以降のスキル継承に生かす必要がある。
ただ、そもそも最優先で継承すべきスキルは何か、そのスキルを備えた人材は誰か、といったことを組織内でディスカッションして計画的に進められる企業はまだ少ない。
やはり、製造業では先輩から自然と学ぶという仕方でスキルが伝えられることが多い。
山川隆史氏(以下、山川氏) 製造業の経営層も、スキルの継承を非常に重要な経営課題として認識しているところが多い。
しかし、継承の方針を具体的に立てて、現場と意識を共有しつつ取り組みを進めている企業は少数にとどまる。
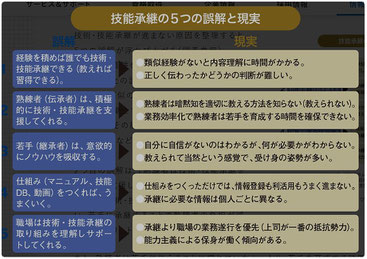
MONOist スキル継承のサイクルを定着化させる上で大事なことは何でしょうか。
高木氏 ポイントは3つある。
1つ目は、先ほども言ったが、スキル継承の対象となるコアなスキルの絞り込みだ。
製造業では部門単位でも数百の技能があり、事業所単位で見れば千、万単位に上ることも珍しくない。それを全て等しく伝えようとするのはそもそも無理がある。
しかも、現場で求められるスキルの種別は不変ではない。技術の進歩や市場のニーズ変化に応じて次々と変わっていく。
一度絞り込んだスキルも、時間がたてば陳腐化してしまう可能性があることには注意すべきだ。
2つ目は、スキル継承のプロセスを計画的に実行することだ。
経営層が課題感を持っていても、実際の現場は日々の生産や開発のオペレーションに忙殺されている。
高度化する顧客要望に応えるためにも、他人にスキルを伝えることより、自分のアウトプットに注力せざるを得なくなってしまう。若手も、自分が何を学ぶべきかが明確でないので、教えてほしいと言い出しにくい。
3つ目は、スキルを学んだ後の効果の可視化だ。
学習者が内容を理解できたか、実際に学習成果を発揮しているかを見える化しないと、教えたが特に変化がない、など「やりっぱなし」になりかねない。
それでは、指導側も何が変わったのかよく分からず、継承活動自体が衰退していくリスクがある。
PDCAの「計画」「実行」「検証」の各ステップで課題を洗い出して、組織としてサイクルを回すことが大事だ。
「コアなスキル」の見極めを
MONOist スキル継承の効果を可視化するために、どのような仕組みが求められるでしょうか。
高木氏 まずはスキル継承の計画の進み具合を可視化する必要がある。
コアなスキル全体に対して、継承計画を作成できているものが全体の何割に及ぶかを見える化する。
その後は計画の進捗率や遅延率の見える化が大事になる。進捗が遅れている活動があれば、その原因を特定し、分析していく。
計画のゴールに対して今どのあたりにいるのかをチーム全体で明確にすることが大事だ。
スキルによっては習得に数年単位かかるものも多く、その成果を把握しやすくしなければならない。
進捗の可視化ではデジタルデータ活用が大切だ。
スキル保有者のデータと計画の進捗度を掛け合わせることで、「どの組織で計画遅延が生じているのか」が浮かび上がってくる。個人単位ではなく、組織や事業所単位で傾向を把握することで、スキル継承を組織的なマネジメントとして進められるようになる。
MONOist 「コアなスキル」かどうかを、どのように見極めればよいのでしょうか。
高木氏 何がコアなスキルかは企業によって異なるので一概に言えないが、まず数日教えれば習得できるようなスキルは、継承プロセスでの優先度を下げてよいだろう。
スキルの中には「この技術は○○さんにしかできない」といわれるものもあるが、実は属人化しているだけで、マニュアル化すれば他の人でもできることもある。
これも優先度を下げていいだろう。
反対に、継承の優先度が高いスキルは何かというと、工場の操業や製品品質に大きな影響を与え得るトラブルの解決手法に関する知見などはその1つといえるだろう。
頻繁に起こるわけではないので、対応可能な人が限られてしまうが、確実に伝えていかなければならないものだ。
この他、例えば溶接など、その企業にとって重要な技術だがまだ自動化が難しく、人手で担うことが求められるスキルなども優先度は高い。
このように選別すると、膨大なスキルの中で、優先すべきものを一気に10%以下にまで絞り込めることもある。
自動化や外注が可能なものは、適宜、必要性を吟味して対応していくべきだ。絞り込みにおいてはデータ活用が大事な役割を果たす。
MONOist 具体的にどのような点でデータが使えるのですか。
高木氏 有効性が一番分かりやすいのが、スキルを保有する人材の年齢のデータだ。
熟練工が定年退職で会社を去れば、その人が持つスキルがリソースとして使えなくなる。
何年後にどのようなスキルを持つ人が退職する可能性があるのか、データをつなげることで把握できれば、対策も打てる。スキルの消失リスクに応じて、継承の優先度を調整することもできるだろう。
MONOist スキルのデータ基盤整備はどう進めればよいでしょうか。
高木氏 いきなりデータを蓄積し始めると、粒度がまちまちでうまく活用できないということになりがちだ。
まずはスキルデータの体系化に取り組むべきだ。
われわれは「スキルの切り口」と呼んでいるが、特定のスキルがどのカテゴリーに属し得るか、どのような枠組みの中に位置付けられるかを考える。
業務プロセスやアウトプットの分類といった観点で切り分け、スキルデータを網羅的に体系化する。
組織全体で共通で機能し得るスキルも洗い出すべきだ。
これまで製造業では、社員のスキルを現場ごとに独自のやり方で設定、管理していた。データが細分化し、スキル継承への活用を阻む障壁となっていた。
バラバラな評価基準を統一化せよ
MONOist 継続的な取り組みにするには、個人の習熟度を客観的に評価する仕組みも必要かと思います。
高木氏 習熟度の判定はこれまで現場ごと、場合によっては個々人で行われてきた。さらに評価の設計も、3段階評価だったり、10段階評価だったりとバラバラだった。
ここをしっかり統合していく必要がある。
習熟度の評価指標を設計する上では、具体性のある、定量的な基準を設けなければならない。
個々人が曖昧な基準で「この人は上級者」「この人はまだ中級者」などと評価していると、同じスキル評価のはずなのに、実際の能力にばらつきが出てしまうという事態になる。
基準としては、業務の経験回数などを指標にするのが分かりやすいだろう。その上で、評価のためにはスキル関連のデジタルデータを活用することが大事になる。
例えば、溶接の技能が「レベル1」の技術者が「レベル2」にステップアップするには、特定の作業を何回こなしたか、何年間業務に従事したかを把握する必要がある。
こうした個々人のデータを一元的に管理する基盤を作り、同一評価の技術者のレベル感がしっかりそろっている、という状況を作る。
最近では、製造業の中でもこの重要性が徐々に理解され始めているように感じる。
また、スキルを十分に職場で活用するには、それを基礎づける教育や、公的/社内資格が重要なことが少なくない。
だが、スキルと教育、知識、資格といったものが互いに持つ関係性が明文化されていないケースもある。そうした条件付けを明確にする必要もあるだろう。
山川氏 習熟度を評価する仕組みは重要だが、人事評価制度の改革にまで組み込むとなると、なかなか取り組みがセンシティブなものになる。
制度改革に着手しているところもないことはないのだが、現時点ではあくまで構想としては持っている、という企業が多い。
定着化に必要な「称賛とルール化」
MONOist デジタルデータを活用する上では、データ入力など現場の協力も不可欠になるかと思います。
現場を巻き込みつつスキル継承の取り組みを定着化させるには、どうすればよいでしょうか。
高木氏 1ついえるのは、スキル関連のデータ基盤やシステムを単体で運用するのではなく、製造プロセスのシステムなど、他システムと連携するところまで視野に入れて考えるべきだということだ。
ある企業では、製造実行システム(MES)と作業者の資格やスキルのデータを連携させることで、作業に必要な特定の資格やスキルがない技術者が業務をしようとすることを防ぐシステムを構築している。このように、現場にとって必要な仕組みが何かを見極めて、それに応えるものを導入することが大事だ。
山川氏 継承プロセスの継続には、スキルデータを最新のものに更新していく必要がある。
このためにも、私は継承のプロセスは「称賛とルール化」がないとうまく回らない、と考えている。「称賛」というのは、育成する側とされる側を両方“褒める”ことだ。
これまで製造業の人材育成は、育てる側も育てられる側も「やって当たり前」という雰囲気があり、育成者が育てただけで褒められることは少なかったのではないか。
スキルのデジタルデータが集まれば、スキル継承全体のどれくらいを自身の育成で進めることができた、こうしたスキルまで習得させることができた、など進捗を可視化できる。これをしっかり評価することで、データ活用に対する育成者のモチベーションを高められる。
一方で、ある程度の強制力を持ってシステムを運用していくことも大事だ。これが「ルール化」に当たる。
事業所の技術教育を担う部門で話を聞いていると、スキルデータ活用の重要性に対する意識と、現状に対する危機感は本当に高まっていると感じる。
一方で、実は最近、経営層や管理職だけでなくメンバー層からも、スキルデータの可視化を好ましく思っているという話を聞く。
職場全体で必要とされているスキルを網羅的に見られる上、自身の先のキャリアを見通す上でも役立つという意見だ。
スキルを軸に上長とキャリアについて話す機会ができたという話も聞く。
スキルデータの整備は、現場の幅広い人材から価値を認めてもらえる取り組みだと思う。
Copyright © ITmedia, Inc. All Rights Reserved.

最後までお読みいただき、有り難うございました。 ☚ LINK
*** 皆さんからの ご意見・ご感想など 『
※ メール・BLOG の転送厳禁です!!
よろしくお願いします。
コメントをお書きください